CASE STUDY
FABRICATED ALLOY PIPING FOR THE COAL-FIRED POWER GENERATION INDUSTRY
When a customer in the power generation industry required specially fabricated piping for a custom pipe spool system, they turned to the expert pipe fitters at Globe. Though many pipe fabricators shy away from working with difficult alloys, we specialize in it. This custom alloy piping is constructed of 2205 duplex stainless steel.
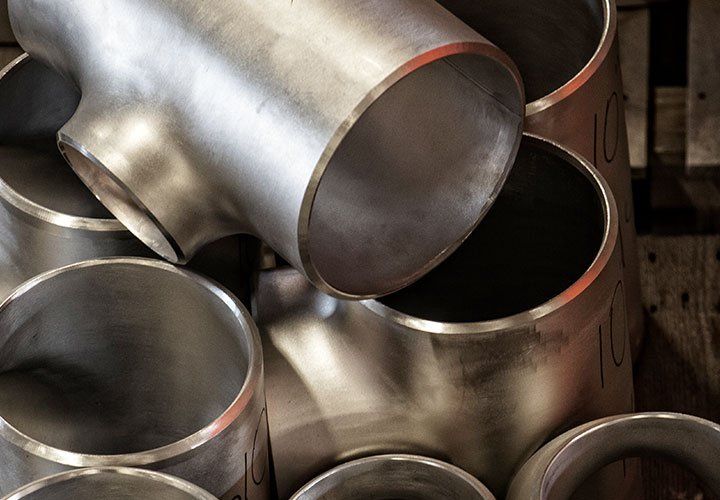
STRONG WELDS FOR CHALLENGING METAL
Due to the combination of austenitic and ferritic structure in the steel, proper welding can be quite challenging. All aspects of the weld must be carefully controlled including the cooling rate of the weld and heat affected zones. If any mistakes are made, the weld joint can lose strength and corrosion resistance (too ferritic) or become brittle (too austenitic). Our ASME certified welders are experienced in making difficult welds and understand the factors involved in creating a strong, quality pipe weld. All ASTM and ASME 31.3 procedures for pipes were strictly followed.
For this project, varying sizes of pipe were fabricated to tolerances of 1/16″. All pipes were 100% visually inspected for weld defects, and 10% of pipes were checked by a third party using radiographic (x-ray) inspection methods. The total turnaround time on this project was 6-8 weeks to our customer in Texas. For more information about this custom pipe spool system project, see the table below, or contact us directly.
PROJECT DETAILS
Specifications | |
---|---|
Product Description | Fabricated Piping for a Pipe Spooling System |
Custom Pipe Fabrication Capabilities Applied / Processes | ASME Welding |
Tightest Tolerances | ± 1/16" |
Material Used | 2205 Duplex Stainless Alloy |
In Process Testing/Inspection Performed | 10% Third Party Radiographic Inspection, 100% Visual Inspection, NDE Testing |
Industry for Use | Coal-Fired Power Generation Plants |
Delivery / Turnaround Time | 6 - 8 weeks |
Delivery Location | Texas |
Standards Met | ASME (American Society of Mechanical Engineers), 31.3 ASTM (American Society for Testing and Materials) 31 |
Product Name | Fabricated 2205 Headers |